Sa., 24.10.20 | 16:00 Uhr
Das Erste
Aus grau mach grün: Grüner Stahl
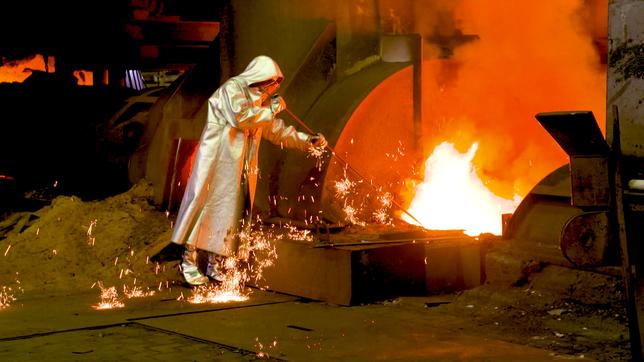
Die Industrie ist der zweitgrößte Treibhausgas-Verursacher in Deutschland. Besonders die Stahlhersteller tragen zur schlechten CO2-Bilanz bei. Das liegt an dem immensen Kohleverbrauch der Hochöfen. Auf eine Tonne produzierten Stahl kommen zwei Tonnen Kohlendioxid. In Deutschlands größter Stahlhütte, bei Thyssenkrupp Steel in Duisburg, wollen die Verantwortlichen jetzt neue Wege gehen – weg von der Kohle hin zu einer CO2-freien Stahlproduktion. Das jedoch ist ein absoluter Bruch mit existierenden Produktionsabläufen.
Denn bislang war Kohle in der Stahlherstellung unersetzlich: Sie liefert nicht nur die Wärmeenergie, die im Hochofen nötig ist, um das Eisen aus den Eisenerz-Pellets heraus zu schmelzen, sie sorgt auch für eine zwingend benötigte chemische Reaktion. Denn Eisen kommt in der Natur hauptsächlich in oxidierter Form vor, also in einer Sauerstoff-Eisen-Verbindung. Dieses oxidierte Eisen lässt sich jedoch nicht verarbeiten. Um Stahl herzustellen, brauchen die Fachleute reines Roheisen.
Dem Sauerstoff muss darum ein alternativer Partner angeboten werden, damit es sich vom Eisen löst und eine andere chemische Verbindung eingeht. Jahrhundertelang war das die Kohle. Über einige Zwischenstufen entstand im Hochofen zum Beispiel aus dem Eisenoxid Fe3O2 in Verbindung mit dem C (Kohlenstoff) der Kohle reines Eisen und CO2. Da das klimaschädliche Treibhausgas CO2 aber künftig vermieden werden soll, sind die Stahlkocher auf der Suche nach einer neuen Rezeptur.
Wasserstoff als Patentlösung
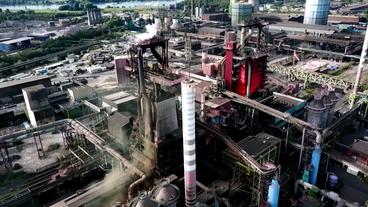
Die Lösung klingt ebenso einfach wie genial: Statt den Hochofen mit einem Erz-Koks-Gemisch zu beladen und zusätzlich fein gemahlenen Kohlenstaub einzublasen, wollen die Stahlhersteller in Duisburg Wasserstoff in den Hochofen pusten. Da Wasserstoff extrem reaktionsfreudig ist, wird er dem Eisenoxid den Sauerstoff entreißen und sich mit ihm zu H2O verbinden – reinem Wasser also, und somit völlig unbedenklich für Mensch und Natur. Das Wasser wird dann als Wasserdampf im Hochofen nach oben zischen und über Rohrleitungen abgesaugt werden. Mit der Wärmeenergie des Dampfes könnte man sogar noch heizen. Die Temperaturen, die benötigt werden, um das Eisen zu schmelzen, würden über einen elektrisch erzeugten Lichtbogen am Fuße des Hochofens geliefert.
Doch so einfach, wie es klingt, ist das alles nicht. Denn schon der Umgang mit Wasserstoff ist riskant. Wasserstoff bildet zusammen mit dem Sauerstoff der Umgebungsluft das gefährliche Knallgas, ein hochexplosives Gemisch. Zudem neigt Wasserstoff dazu, mit diversen Reaktionspartnern chemische Verbindungen einzugehen. Die Stahlkocher müssen also dafür sorgen, dass der Wasserstoff erst dort reagiert, wo sein Potenzial gebraucht wird: tief im Inneren des Hochofens. Deshalb haben sich die Ingenieure bei Thyssenkrupp zu einem Versuchsbetrieb der kleinen Schritte entschlossen. Sie rüsten einen konventionellen Hochofen stückweise um.
Den Stahlkochern geht die Düse
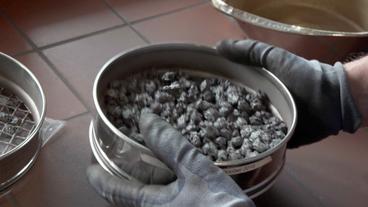
Der "Hochofen 9" des Duisburger Stahlwerks wird nach und nach auf Wasserstoff umgestellt. Genauer gesagt, die Düsen, die im unteren Bereich des Ofens knapp 1.000 Grad heiße Luft und Kohlenstaub einblasen. Derzeit erproben die Stahlkocher an einer Düse, wie sich die Prozesse verändern, wenn statt des Luft-Kohlenstaub-Gemisches reiner Wasserstoff eingeführt wird. Mittelfristig sollen alle 28 Düsen des Hochofens mit Wasserstoff betrieben werden.
Allerdings wird der Ofen zunächst weiterhin mit einer Mischung aus Eisenerz-Pellets und Kohle beziehungsweise Koks befüllt. Und deshalb entsteht bei diesem Prozess auch weiterhin CO2. Die Ingenieure haben aber berechnet, dass sich durch den Einsatz von Wasserstoff der CO2-Ausstoß dabei trotzdem um 30 Prozent verringern lässt. Bis 2030 wollen sie dieses Einsparpotential ausschöpfen.
Die komplett CO2-freie Stahlproduktion wird aber erst mit einem neuen Verfahren realistisch, das bis 2050 entwickelt und in Betrieb gehen soll. Bei Thyssenkrupp heißt das Projekt "Hochofen 2.0". Dieser Hochofen würde nur noch mit Eisenerz und nicht mehr mit einem Koks-Erzgemisch befüllt. Statt vorgeheizter Luft und Kohlenstaub wird dann nur noch Wasserstoff eingeblasen. Die Schmelztemperatur soll über elektrische Energie erzeugt werden. Allerdings sind vorher noch einige Probleme zu lösen. Derzeit hinkt zum Beispiel die Wasserstoffproduktion weit hinter dem neuen Bedarf der Industrie her. Und damit es auch grüner Wasserstoff ist, muss dieser mittels elektrischer Energie – per Elektrolyse gewonnen werden.
Der Weg aus der Krise? - Elektrolyse!
Ein Konzern, der an dieser Wende auf dem Energiemarkt teilhaben will, ist Shell. Der Öl- und Gas-Gigant muss sich neu erfinden. Denn bei steigender Elektromobilität wird die Nachfrage nach fossilen Kraftstoffen vermutlich zurückgehen – und selbst wenn die Nachfrage stabil bleiben sollte: Die vorhandenen Ressourcen sind in jedem Fall endlich. Deshalb erschließt sich der Konzern gerade die Wasserstoffproduktion als neues Geschäftsfeld.
Das Unternehmen baut auf dem Gelände der Shell Rheinland-Raffinerie die größte Elektrolyse-Anlage der Welt. Sie soll 1.300 Tonnen Wasserstoff pro Jahr erzeugen und mittelfristig auf das zehnfache erweiterbar sein. Die EU fördert das Projekt mit zehn Millionen Euro. Die erwarteten 1.300 Tonnen würden aktuell allerdings gerade einmal 1 Prozent des Eigenbedarfs der Raffinerie decken. Denn allein für die Entschwefelung von Kraftstoffen verbraucht die Shell Rheinland gigantische Mengen Wasserstoff. Rund 78 Prozent des benötigten Wasserstoffes gewinnt der Konzern zwar aus Abfallprodukten der Raffinerieprozesse, doch dieser Wasserstoff stammt aus fossilen Energiequellen und ist damit Mitursache für den Klimawandel. Langfristig müssen Alternativen her.
Shell möchte mit dem neuen Elektrolyse-Projekt vor allem Erfahrung im Umgang mit Wasserstoff sammeln, um in Zukunft verstärkt auf diesem Geschäftsfeld mitmischen zu können. Chemisch gesehen, ist der Einsatz von Wasserstoff zur CO2-Vermeidung bestechend einfach und völlig ohne unangenehme Nebenwirkungen. Technisch und wirtschaftlich gibt es aber noch nicht ansatzweise die Infrastruktur oder die Strommengen aus erneuerbaren Energiequellen, um diesen Wandel ernsthaft anzugehen. Die EU hat das erkannt und ein großes Wasserstoff-Förderprogramm aufgelegt. Letztlich geht es bei diesen Prozessen immer nur über den Preis. Wenn der CO2-Ausstoß in Zukunft noch stärker besteuert werden sollte, lohnen sich die konventionelle Stahlproduktion und die Stromerzeugung aus Kohlen, Gas und Öl immer weniger. Die Konzerne erwarten diese Entwicklung und setzten nun verstärkt auf Wasserstoff.
Autor: Björn Platz (NDR)
Stand: 24.10.2020 15:19 Uhr